i-Scup
Repair and reinforcement of reinforced concrete structures using thin layers of UHPC shotcrete: Areas of application, design, durability, processing technology.
In the field of transportation structures as well as building construction, the current building stock is typically 30 to 80 years old. Due to chloride exposure and high traffic loads, the structures are usually in a deteriorated condition. There is currently a very great need for efficient repair and reinforcement methods to adapt the outdated building stock to today's requirements.
By using the innovative high-performance material ultra-high performance concrete (UHPC), an optimized repair and reinforcement system is being developed. The material is used here for the first time as shotcrete (UHPC shotcrete). This technically simplifies and optimizes the construction process. With regard to the static effect, the high-performance material is applied where it can act most efficiently, directly on the surfaces with the greatest possible lever arm. With regard to durability, the dense UHPC can reduce the corrosion process to a harmless level due to the high electrolyte resistance. At the same time, the structure is permanently protected against the penetration of new chlorides.
The load-bearing behavior of the composite system is influenced by the interaction of the existing normal-strength concrete component with the high-strength top concrete layer. The composite behavior and, in particular, the time-dependent material behavior (shrinkage, creep) of the two cementitious materials must be taken into account. The efficient increase in load-bearing capacity results from the very high compressive strength of the UHPC. An increase in the tensile strength of the composite component is also achieved by the fiber-carrying effect of the UHP(FR)C (FR = fiber reinforced) used for this purpose. The application as shotcrete has a favorable effect on the fiber distribution. The fibers align themselves primarily parallel to the surface and this improves the tensile and flexural strength of the composite material. For the absorption of large tensile forces and the achievement of high deformation capacities, it is possible to incorporate additional reinforcing elements (reinforcing steel, prestressing steel, textiles, etc.) into the system.
Due to the steel fibers in UHP(FR)C, multi-crack formation can be generated, comparable to crack-distributing reinforcement. This is achieved by the crack-crossing fibers, which have a higher strength than the surrounding matrix strength. Thus, a crack that has developed does not open further, but secondary cracks are formed (cf. crack distribution in reinforced concrete). The crack spacing is only a few millimeters and the crack width is thus very small. The order of magnitude for UHP(FR)C is 0.02 mm compared to 0.2 mm for reinforced concrete. The aim is that the UHPC layer is thus able to permanently keep chlorides away from the reinforced concrete structure.
The special feature of this research approach is the close interlocking of the design-related and load-bearing capacity-relevant issues with the building material-specific as well as durability-relevant characteristics. In this way, the excellent properties of UHPC in the area of load-bearing capacity and durability are optimally utilized and the material is used in an economically efficient manner.
Research area: | Structural Concrete, Structural Engineering |
Building Materials, Building Preservation | |
Responsible: | Prof. Dr. Jörg Jungwirth |
Prof. Dr.-Ing. Christoph Dauberschmidt | |
Prof. Dr.-Ing. Andrea Kustermann | |
M. Eng. André Strotmann | |
M. Eng. Toni Pollner | |
Funding: | Federal Ministry of Education and Research |
Duration: | 01.04.2019 - 31.10.2013 |
Project partner: | Lafarge-Holcim with Ductal |
Karrié |
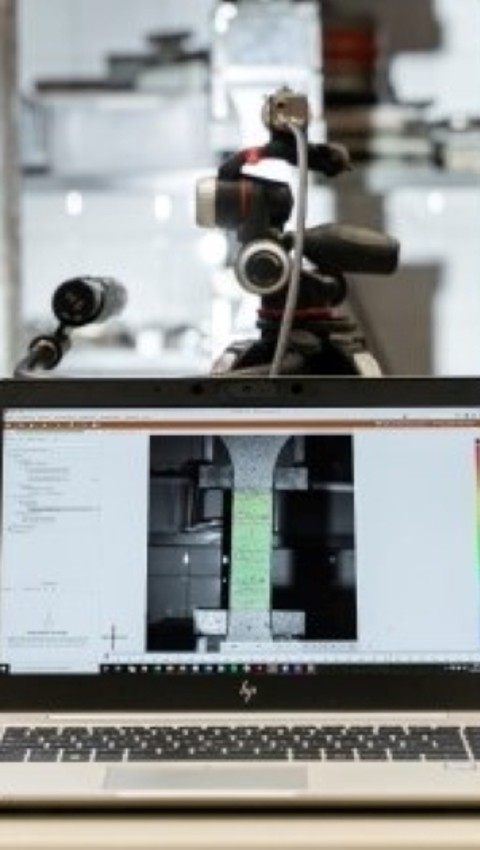