Fiber Reinforced Plastic
Innovative Design and Manufacturing for Fiber Reinforced Plastic Components
Developers and manufacturers of continuous-fiber-reinforced plastic components have to face very great challenges in competition with other lightweight materials, above all in order to minimize material usage and production costs. This begins with the design of the components, which should be as fiber-compatible as possible, with the difficult task of optimally designing the best possible layer structure to achieve maximum strength and stiffness. In addition, the manufacturing process is characterized by high tolerance requirements for low component distortion and high costs due to complex processes for cutting and depositing, combined with a lot of waste of semi-finished products during component manufacture.
In this project, innovative methods are being investigated to significantly improve several aspects of the use of traditional fiber composite structures with continuous fibers through new design principles, design methods and innovative manufacturing technology. Consistent application of these design principles, layout methods and manufacturing techniques leads to better fiber composite components with higher strength and stiffness, as well as lower weight and material usage via more efficient material utilization, significantly less distortion of components in manufacturing and also less waste via a more efficient, because simplified, laydown technique. The methods are suitable for various manufacturing processes, such as RTM or prepreg-based manufacturing. The effort for analysis and optimization is drastically reduced compared to traditional analysis methods.
The methods were developed by a team led by Prof. em. Stephen W. Tsai of Stanford University and a group of international researchers, industry specialists and companies.
Key features of the new methods: Use of only three material parameters for stiffness and strength dimensioning, greatly simplifying the provision of necessary data for design. For the ply structure, two plies each with a double helix - called double-double - are proposed to replace the traditional 0, ±45 and 90° structure. This allows significantly thinner minimum wall thicknesses. Double-Double laminates homogenize with only a few layers and already have symmetrical, distortion-minimizing structural properties even without a symmetrical layer structure. For example, a longitudinally stiff laminate with 20 individual layers [05/±452/90]S can be replaced by a simpler structure with [±0/±50]5T. This makes the deposition technique simpler and more error-free. The deposition of single layers can be done flexibly according to structural-mechanical needs, patchwise and without the need for symmetrical build-up! Laminates can be realized as "orthotropic aluminum" with considerable - exceeding the previous limits - thickness changes over the component surface. Such layer buildups tend to have less microcracking, splitting or delamination. With the use of thin single layers and ondulation-free fabrics (non-crimp fabrics), a new generation of applications with only uniaxial deposition technology can be achieved with unsurpassed strength as well as reduction of required mass and manufacturing costs.
Research field: | Structural Analysis and Integrity |
Responsible: | Prof. Dr.-Ing. Klemens Rother |
Duration: | since 2016 |
Project partner: | Prof em. Stephen Tsai D. Eng., Stanford University, Palo Alto, USA |
as well as numerous other international partners from research and industry |
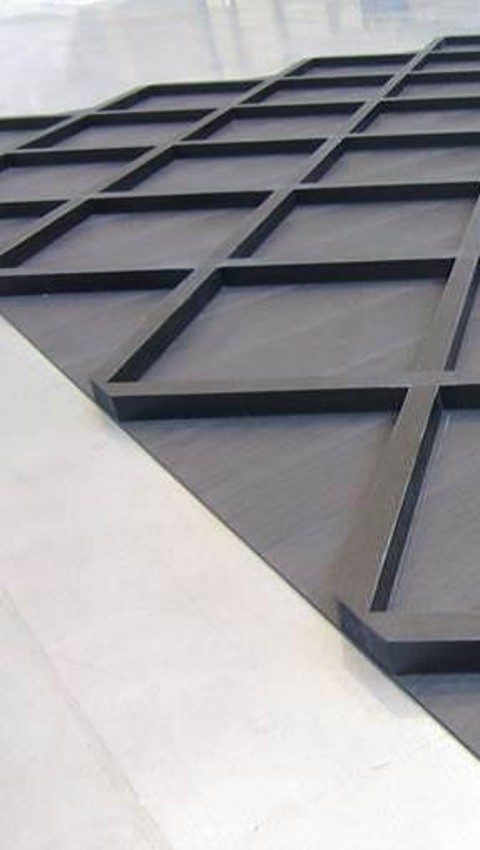