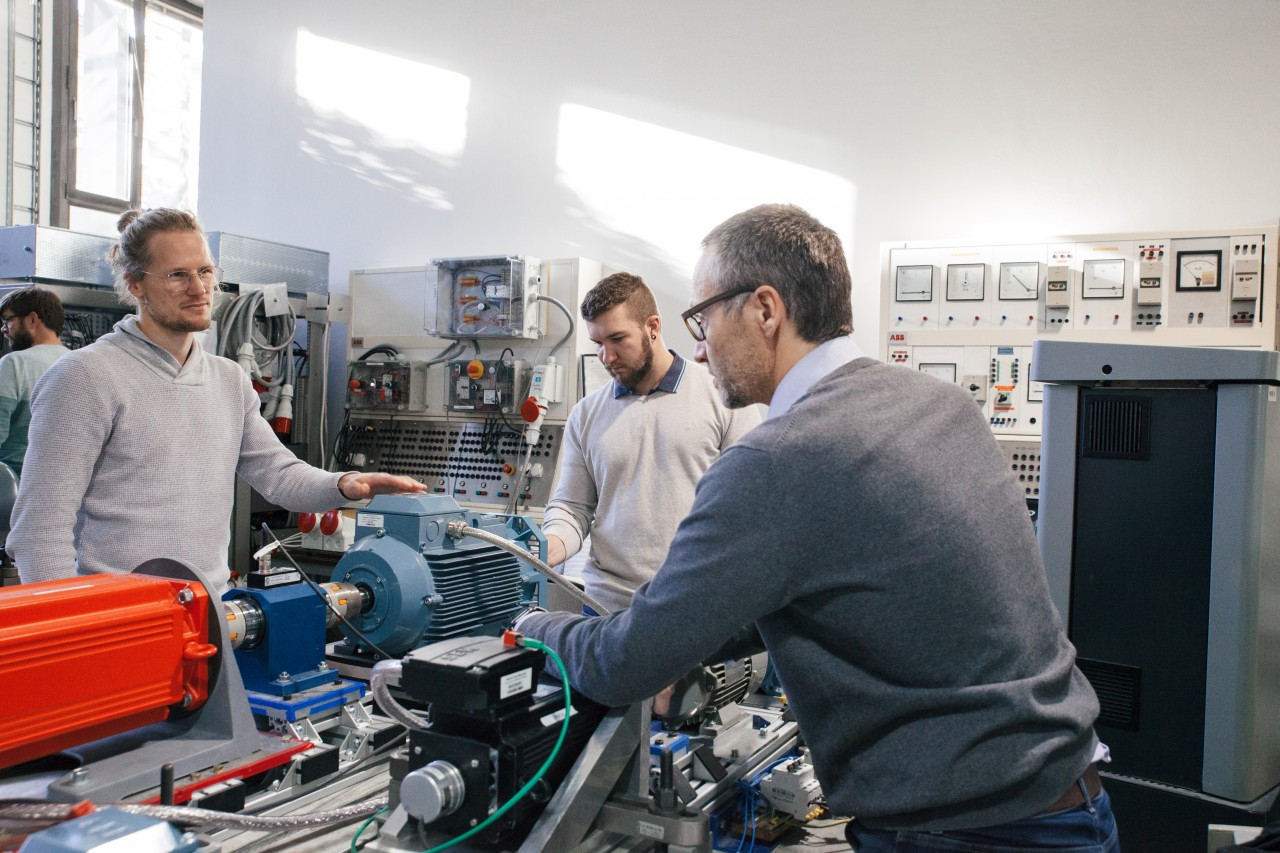
Machine map based modeling, identification and optimal feedforward torque control approach for induction machines
A novel and simple machine map-based modelling, identification and optimal feedforward torque control (OFTC) concept for induction machines (IMs).
It is based on a generic, nonlinear transformer-like machine model that accounts for nonlinear flux linkages (with magnetic saturation and cross-coupling) and iron losses in the stator laminations in a novel, arbitrarily rotating but unambiguous, robust and reproducible (d,q)-reference frame; a holistic machine identification procedure that evaluates steady-state measurements over a grid of (d,q)-stator currents and provides temperature- and frequency-dependent machine maps for e.g. a numerical offline optimization. e.g. a numerical off-line optimisation and extraction of different OFTC look-up tables (LUTs) for an optimal current reference generation depending on reference torque and electrical frequency (and temperature). During identification, the temperature of the stator winding and the electrical stator frequency of the IM are kept constant by an intelligent temperature and speed control system. The presented measurement results for a squirrel-cage IM confirm that compared to constant flux operation or scalar V/Hz control, efficiency can be increased by up to 7% using Maximum Torque Per Losses (MTPL), especially in part-load operation, while minimising copper and iron losses.
Read more details in the published article.